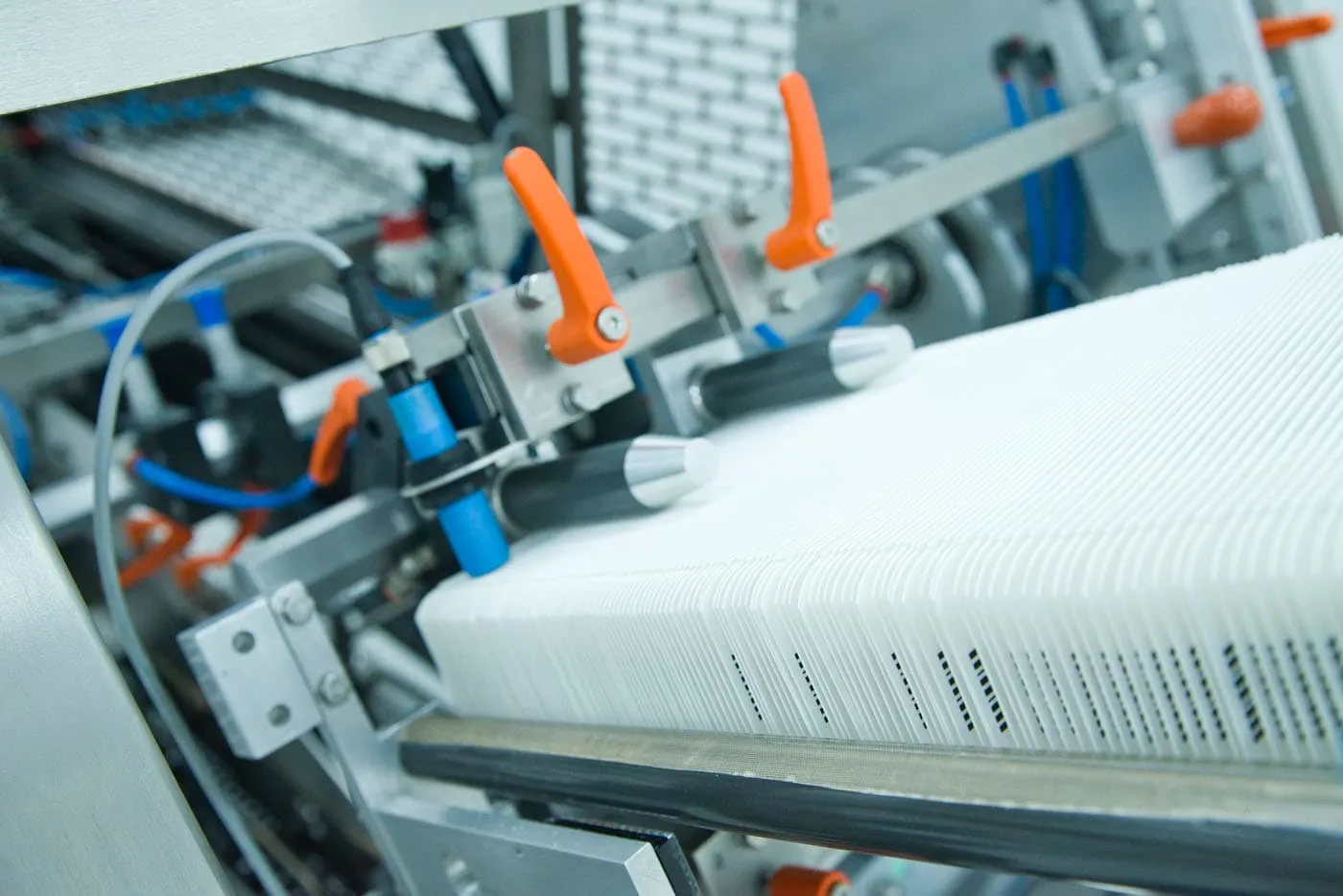
Thermoform packaging machine
What is a thermoform packaging machine?
A thermoform packaging machine is a machine that uses heat to form plastic in a mould. This manufacturing process forms blisters into a specific shape and then trims it. There are different types of thermoforming packaging machines that can be used. For example, if you require only sample and prototype parts, a small lab size machine will suffice, which can heat small cut sections of plastic sheet. If you require high-volume and complex applications and want to produce many thousands of finished parts per hour, you will need to use large production machines to heat and form the plastic sheet. These thermoform packaging machines also trims the formed parts, all in a continuous high-speed process.
How do thermoforming packaging machines work?
As mentioned before, a thermoform packaging machine works with forming blisters in a specific shape. The process is as follows: a sheet of plastic is heated in an oven to a temperature that is high enough for stretching into or onto a mould, after which it is cooled down. When the thermoforming is done using a large machine, the plastic sheet is transported through an oven using a set of indexing chains that pierce the sheet, which is fed continuously from a roll. After this, the heated sheet is transported to a forming station where it is placed between a mould and pressure box. These close on the sheet. Simultaneously, a vacuum, along with pressurised air, makes sure any trapped air is removed, and the plastic sheet is pulled into or onto the mould to fit the shape perfectly. After this, the excess material is trimmed and stored, to make sure it can be recycled.
The different types of thermoforming
Vacuum Forming: A plastic sheet within a frame is heated until it becomes highly flexible. A vacuum extracts the air, forcing the sheet into a mould. This fast and cost-effective process is perfect for high-volume projects.
Pressure Forming: Following steps akin to vacuum forming, pressure forming incorporates an additional tool that presses the part into place while the vacuum removes air. This method yields more detailed pieces with consistent plastic thickness.
Drape Forming: In this technique, the heated plastic sheet is draped over or pressed onto a mandrel or form. Though less precise, it is an ideal option when cost is a primary concern, as it requires minimal tooling or fixtures. However, lower costs come at the expense of accuracy.
Billow Forming: Also known as "free forming," this method does not use a mould. Instead, air jets blow the heated plastic into a bubble, making it suitable for constructing domes or skylights.
Matched Mold Forming: This process employs both male and female moulds to shape a part precisely. While highly detailed, matched mould forming entails higher tooling costs due to the need for additional components.
Twin Sheet Forming: Two layers are heated and shaped simultaneously before being combined to form a single piece. This technique is optimal for creating double-walled and hollow items.
The advantages of a thermoform packaging machine
- Quick and easy process: the mould and pressure box ensure that the plastic sheet can quickly and easily be formed in the desired shape.
- Suitable for nearly all types of plastic: different types of plastic have different properties. Most thermoplastics are suitable for a thermoform packaging machine.
- Sturdy material: the plastic that is used in thermoforming is sturdy, making it ideal for different types of blister packaging.
- Versatile: the plastic sheets can be formed into or onto any shape mould, making the thermoforming packaging machine very versatile.
Get a free Locked4Kids carton sample now!
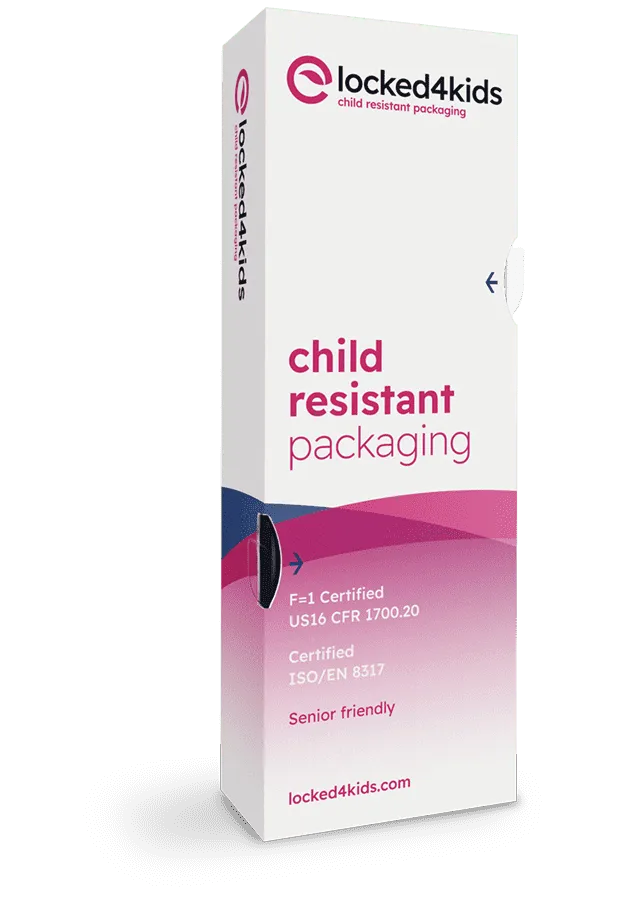
- Child resistant, senior friendly
- ISO/EN 8317 and US16 CFR 1700.20 certified
- Available in a range of sizes and applications
Your sample request has been sent! You'll get a confirmation at the provided email address.